O systemach sterowania czy rozwiązaniach napędowych myślimy zazwyczaj w kontekście ich wdrażania oraz uruchamiania w danej maszynie czy obiekcie przemysłowym. Wykorzystywane w nich komponenty są też zwykle traktowane jako podstawowe elementy składowe, z których automatycy dopiero tworzą rozwiązanie. Z drugiej strony, same w sobie są złożonymi, sprzętowo-
-programowymi systemami, a ich początki mogą być znacznie odleglejsze i sięgać – jak ma to miejsce w przypadku firmy Mitsubishi Electric – centralnego regionu Japonii.
[dropcap]P[/dropcap]rzedstawiamy dwa nowoczesne zakłady japońskiego koncernu, w których produkuje się gamę urządzeń automatyki i sterowania. W obiektach tych wdrożono nowe lub zreorganizowano dotychczasowe procesy wytwarzania, automatyzując i robotyzując produkcję. Korzystając z okazji, rozmawiamy z osobami odpowiedzialnymi za tworzenie oferty firmy i dyskutujemy, jak na rozwój produktów wpływa dzisiaj konieczność zdalnego udostępniania danych oraz integracji automatyki z systemami IT.
Mitsubishi to w Polsce marka znana głównie z klimatyzatorów, pojazdów oraz z automatyki przemysłowej. Zanim porozmawiamy o tej ostatniej i sposobach jej wytwarzania, poprosiłbym o nakreślenie szerszej perspektywy dotyczącej koncernu.
Poza granicami Japonii rzeczywiście często jesteśmy kojarzeni z produktami takimi jak wymienione, aczkolwiek zakres działalności Grupy Mitsubishi jest znacznie szerszy. Skupia ona ponad 200 przedsiębiorstw, w tym działającą w przemyśle lotniczym i kosmicznym Mitsubishi Heavy Industries, znanego producenta sprzętu fotograficznego, którym jest Nikon, a także drugą globalnie grupę finansową Mitsubishi UFJ Financial Group. Mitsubishi ma też własny browar – Kirin Brewery, dzięki czemu po pracy również możemy wspierać naszą firmę(!). Występowanie tego typu konglomeratów, określanych jako keiretsu, to unikatowa cecha rynku japońskiego.
Rozwojem i produkcją automatyki przemysłowej zajmuje się Mitsubishi Electric. Ta ostatnia składa się pod względem wartości sprzedaży na około 26% rocznych obrotów firmy, stanowiąc jednocześnie największy z obsługiwanych przez nas sektorów rynku. Drugim, o podobnej wielkości, jest ten związany z systemami elektrycznymi i energetycznymi.
Działamy globalnie – na świecie mamy ponad 40 centrów factory automation, zaś sprzedaż produktów i wsparcie usługowe zapewniane jest w około 600 lokalizacjach. Również w zakresie produkcji korzystamy z sieci zakładów, przy czym kluczowe są dla nas te w Japonii. Mamy ponad 90 lat doświadczeń w wytwarzaniu automatyki i dzielenie się tym know-how z klientami traktujemy jako element naszej misji.
Jakie są obecnie wyzwania rynkowe i technologiczne, patrząc z perspektywy globalnego dostawcy automatyki przemysłowej?
Obserwujemy wiele zmian, które dzisiaj często określa się zbiorczo mianem czwartej rewolucji przemysłowej. Z punktu widzenia dostawcy automatyki wymagają one tworzenia urządzeń, które łatwo będzie integrować w większych systemach i które zapewnią wartość dodaną dla użytkownika – np. w zakresie przetwarzania informacji czy łatwej komunikacji z systemami IT. Ponieważ produkty te trafiają do instalacji, gdzie wykorzystywane są również starsze podzespoły, naszą rolą jest też zapewnianie ich kompatybilności wstecznej.
Propozycją Mitsubishi Electric jest tutaj rozwiązanie e‑F@ctory, czyli zestaw technologii i produktów zapewniających możliwość integracji sterowania, wymiany danych oraz ich analizy od poziomu produkcyjnego do zarządzania przedsiębiorstwem. Rozwijamy je od dekady i, pod względem koncepcyjnym, jest ono podobne do dzisiejszego Industry 4.0. Istotnym elementem e‑F@ctory jest platforma automatyki iQ, łącząca kontrolery, sieci komunikacyjne oraz jednolite oprogramowanie nadrzędne. Stanowi ona nie tyle zbiór komponentów, lecz kompletne rozwiązanie, które pozwala firmom zwiększać produktywność i integrować świat automatyki z obszarem IT.
Przykładem na to ostatnie jest wdrożenie zrealizowane przez Technikon Limited dla spółki Russian Railways. Polegało ono na rozbudowie zakładu serwisowania taboru kolejowego, gdzie w sposób ekstensywny wykorzystano omawianą platformę – jako jedyną spełniającą wymogi klienta. iQ używana jest zarówno do sterowania i kontroli maszyn oraz robotów, jak też do pełnego raportowania i wymiany danych z systemami informatycznymi. W omawianej aplikacji system m.in. determinuje konieczny zakres serwisowania wózków jezdnych w oparciu o dane automatycznie zbierane podczas użytkowania taboru. Obecnie modernizacji podlegają kolejne zakłady w kraju.
Porozmawiajmy o specyfice produkcji urządzeń automatyki. W Nagoi, w centralnym regionie Japonii, zlokalizowany jest największy kompleks produkcyjny Mitsubishi Electric. Co w nim wytwarzacie?
Nagoya Works to główne miejsce rozwoju produktów automatyki i rozwiązań z zakresu e‑F@ctory. Prowadzimy tu istotną część działalności R&D [Research and Development – opracowanie i wdrażanie nowych produktów i usług, a także wszelkiego rodzaju projektów i przedsięwzięć; przypis red.], świadczymy także usługi wsparcia klientów – w tym w zakresie tworzenia aplikacji. Głównym profilem działalności obiektu jest jednak wytwarzanie szerokiej gamy urządzeń automatyki, elektrotechnicznych oraz maszyn. Ogółem jest tu zatrudnionych ponad 7 tysięcy pracowników.
W zakładzie w Nagoi, który powstał ponad 90 lat temu, wytwarzane były początkowo silniki elektryczne. Jego dynamiczny rozwój nastąpił pod koniec lat 70. ubiegłego wieku, kiedy rozpoczęła się produkcja sterowników programowalnych. Wtedy też do Nagoi została przeniesiona produkcja urządzeń CNC [Computerized Numerical Control – komputerowe sterowanie urządzeń numerycznych; przypis red.], a rok później również maszyn do cięcia laserowego. W następnej dekadzie nastąpił rozwój kolejnych produktów z zakresu factory automation – m.in. robotów oraz serwonapędów sterowanych cyfrowo. Na terenie kampusu powstało też FA Communication Center, świadczące usługi wsparcia dla klientów oraz innych centrów, zlokalizowanych na całym świecie.
Dzisiaj w Nagoya Works wytwarzamy wszystkie wymienione produkty, a oprócz tego również kontrolery automatyki, panele operatorskie oraz urządzenia elektroenergetyczne. Powstaje tu także szereg urządzeń napędowych – silników elektrycznych, przemienników częstotliwości, systemów numerycznych oraz serwonapędów. Spora jest nie tylko gama produktów, ale też skala ich produkcji. Samych PLC [Programmable Logic Controller – Programowalny Sterownik Logiczny, czyli uniwersalne urządzenie mikroprocesorowe, przeznaczone do sterowania pracą maszyny lub urządzenia technologicznego; przypis red.] wytwarzanych jest obecnie ponad 300 tys. sztuk miesięcznie!
W kompleksie produkcyjnym znajduje się również budynek z pomieszczeniem showroom, w którym organizujemy prezentacje i szkolenia dla klientów. Oprócz przeglądu wytwarzanych produktów można w nim zobaczyć kompletne aplikacje – przykładowo systemy montażowe z robotami sześcioosiowymi. Te ostatnie, dzięki zastosowaniu odpowiednich czujników i systemu wizyjnego, wykrywają pozycję oraz układ elementów przed ich pobieraniem. System sterowania i kontroli maszyny bazuje w tym przypadku na platformie iQ.
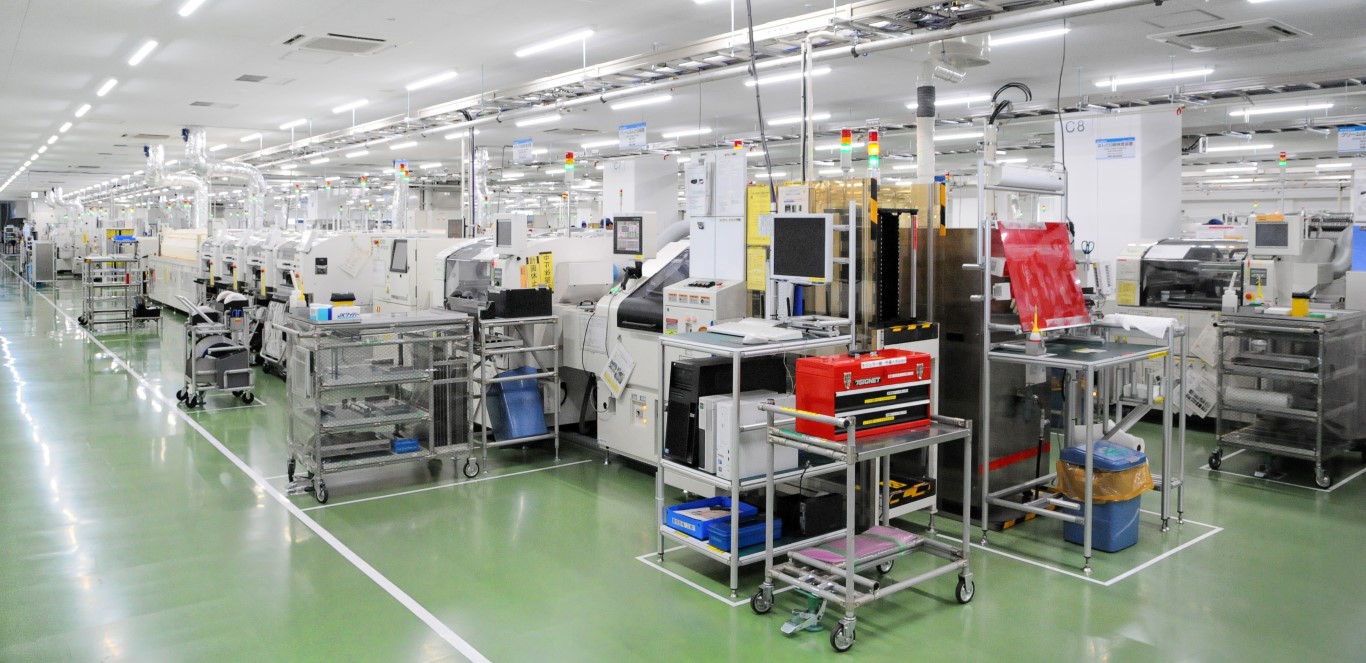
Nagoya Works to dla Mitsubishi Electric główne miejsce projektowania i wytwarzania urządzeń automatyki, elektrotechnicznych oraz maszyn. W kompleksie produkcyjnym zatrudnionych jest ponad 7 tys. osób, tutaj również świadczymy wsparcie dla innych naszych centrów Factory Automation.
Jesteśmy w budynku E4 – najnowszym z obiektów na terenie zakładu. Co jest tutaj wytwarzane i jak zorganizowana jest produkcja?
To nasz najnowszy obiekt produkcyjny, gdzie wytwarzamy sterowniki programowalne, panele operatorskie oraz, w mniejszej skali, podzespoły mocy do przemienników częstotliwości i enkodery [przetworniki obrotowo-impulsowe, przeznaczone do pomiaru przemieszczeń kątowych, a więc zarówno do pomiaru kąta, jak i prędkości kątowej; przypis red.]. Produkcja w E4 rozpoczęła się w połowie 2014 roku. Budynek ma sześć pięter i powierzchnię 26 tys. m2, co daje dosyć duże możliwości produkcyjne. Działa w nim 16 linii produkcyjnych, z czego 12 przeznaczonych jest do wytwarzania PLC.
Produkcja sterowników czy HMI [Human-Machine Interface – Interfejs Człowiek-Maszyna, czyli ogół składników służących do obsługi urządzenia przez człowieka; przypis red.] to w istocie wytwarzanie elektroniki profesjonalnej, stąd też stosowane przez nas procesy są dosyć typowe dla tego typu cyklów. Korzystamy z montażu powierzchniowego elementów, które są automatycznie nakładane, podobnie jak pasta lutownicza. Na tym etapie odbywa się kontrola wizualna, kolejna następuje po przejściu płytek przez piec lutowniczy. Następnie półprodukty są transportowane na kolejne piętro z wykorzystaniem systemów transportu pionowego, gdzie ręcznie są montowane większe komponenty. Pracownicy mają zapewniony podgląd procedury na monitorach, co sprzyja poprawności tego procesu. Korzystamy również ze zrobotyzowanych linii do montażu, używanych w przypadku sterowników iQ-R. Płytki elektroniczne przechodzą testy na odporność temperaturową, a po ich zainstalowaniu w obudowach dodatkowo też m.in. testy odporności na wibracje.
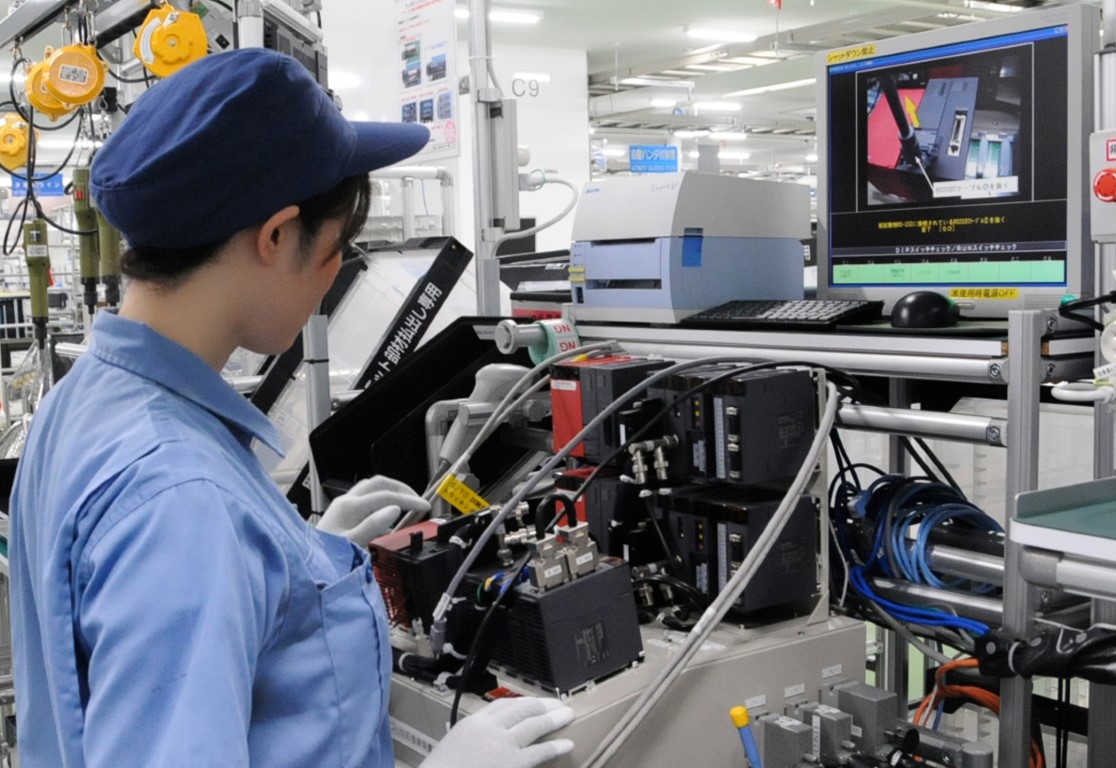
Produkcja i montaż sterowników PLC, HMI i innych produktów automatyki w Nagoi.
Wracając jeszcze do samego budynku, warto dodać, że jego instalacje zostały wyposażone w rozwiązania z zakresu e‑F@ctory, a ich pracę nadzoruje system BMS [Building Management System – System Zarządzania Budynkiem, co oznacza zarządzanie systemami automatycznego sterowania w budynku, zwłaszcza w budynku inteligentnym; przypis red.]. Pozwala on na udostępnianie danych o działaniu m.in. systemu HVAC [system klimatyzacji i wentylacji; przypis red.], instalacji oświetleniowej, a także raportowanie informacji z produkcji. System zapewnia też raportowanie zużycia energii zarówno lokalnie, jak też zdalnie przez internet.
Budynek przedstawiacie nie tylko jako referencyjny projekt w zakresie organizacji procesów produkcyjnych, ale też budownictwa odpornego na trzęsienia ziemi. Problem ten w niewielkim stopniu występuje w Europie – jak istotny jest on w tym regionie?
Japonia jest obszarem o dużej aktywności sejsmicznej – również w obszarze Tokai, gdzie się znajdujemy, spodziewane są w przyszłości dosyć silne trzęsienia ziemi. W przeszłości wydarzenia te miały duży wpływ na produkcję przemysłową w naszym kraju – wystarczy choćby wspomnieć problemy branży motoryzacyjnej po trzęsieniu ziemi i tsunami w marcu 2011 roku. Dlatego też podjęto decyzję, aby nowy budynek w Nagoi, jako że wytwarzamy tutaj nasze najbardziej zaawansowane urządzenia automatyki, był obiektem o wysokiej odporności na anomalie sejsmiczne.
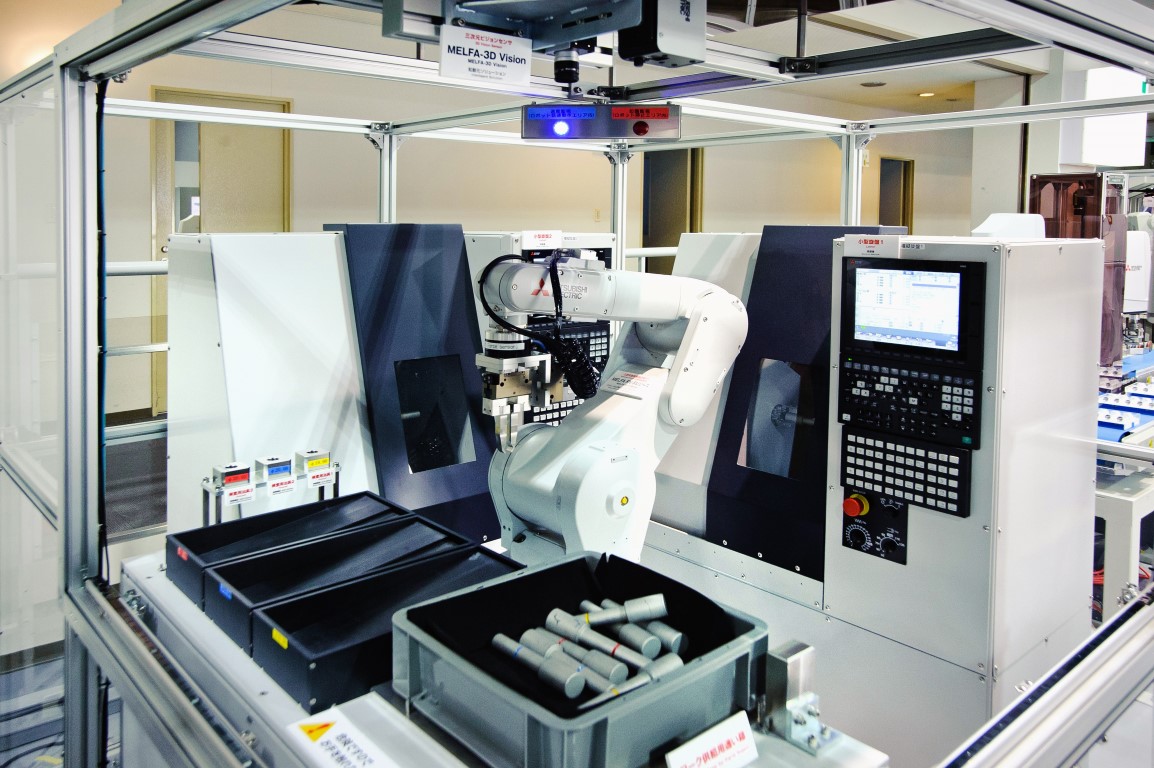
Showroom w Nagoya Works – widoczne m.in. maszyny i roboty przemysłowe ze zintegrowanymi systemami wizyjnymi, sterowane z wykorzystaniem platformy iQ.
Cały obiekt usadowiony jest na 73 kolumnach znajdujących się na tłumikach drgań sejsmicznych – w dużej części o średnicy jednego metra. Są to elementy wykonane ze stalowych pierścieni znajdujących się w gumie i charakteryzujących się bardzo dużą wytrzymałością w pionie, przy jednoczesnej elastyczności poziomej. Jeden tłumik może utrzymać obciążenie do tysiąca ton, przy jednoczesnej możliwości wychylenia do 60 cm w płaszczyźnie X–Y. Oprócz nich zastosowano kilkanaście tłumików w kształcie litery U, mających za zadanie absorbować energię wstrząsów i tłumić wibracje. Takie rozwiązanie zapewnia redukcję wibracji budynku na skutek trzęsienia ziemi o połowę w przypadku parteru i aż do 80% w przypadku szóstego piętra.
W piwnicy, gdzie znajdują się tłumiki drgań, widać również luźne połączenia kablowe – są one niezbędne, aby zapewnić niezawodność połączenia elektrycznego podczas wstrząsów. Podobnie jest z instalacjami hydraulicznymi, które są po części wykonane z połączeń elastycznych. Na wypadek problemów z dostawami energii budynek wyposażony jest w generatory rezerwowe oraz instalację fotowoltaiczną.
Obiekt zapewnia możliwość uruchomienia produkcji kolejnego dnia po wystąpieniu dużego trzęsienia ziemi. Stanowi on ważny element naszego planu zarządzania ryzykiem w zakresie ciągłości łańcucha dostaw na rynkach lokalnym i zagranicznych. Budynek pełni również ważną funkcję lokalną – w przypadku zagrożenia może służyć jako centrum kontroli kryzysowej, dając pracownikom możliwość kilkudniowego, bezpiecznego schronienia.
Przenieśmy się do odległego o 40 km zakładu produkcyjnego w Kani. Jest to mniejsza fabryka, o zupełnie innym profilu produkcji – wytwarzana jest tu aparatura łączeniowa niskiego napięcia i elementy mechatroniczne. Jak zorganizowane są procesy produkcyjne i z jakimi wyzwaniami musieliście się zmierzyć?
Zakład w Kani ma krótszą historię niż kompleks w Nagoi, jest znacznie mniejszy, a także różni się profilem działalności. Jego głównymi produktami są styczniki, które uzupełniane są przez przekaźniki i inną aparaturę łączeniową. Te pierwsze są Mitsubishi dla o tyle istotne, że w ich rynku w Japonii mamy około 40-procentowy udział. Dekadę temu pracownicy zakładu świętowali wyprodukowanie 100-milionowego stycznika!
Omawiany produkt przeszedł przez kilka dekad produkcji szereg zmian – dzisiaj wytwarzamy w Kani jego 14. generację. Wytwarzanie tego typu aparatury różni się jednak znacznie od produkcji wyrobów wysokomarżowych. W przypadku styczników i innych produktów elektromechanicznych musimy być w pełni skupieni na osiąganiu doskonałości operacyjnej, a więc zapewnianiu jakości procesu produkcyjnego i optymalizacji jego kosztów. Podczas montażu korzystamy z oznaczeń kodowych elementów składowych i stosujemy śledzenie całej produkcji, co zapewnia nam pełne dane indywidualnego produktu. Jest to o tyle ważne, że wytwarzamy bardzo dużą liczbę wersji i konfiguracji wyrobów – w przypadku styczników jest ich aż 14 tysięcy, dzięki czemu nie ma miejsca na pomyłki.
Do wytwarzania styczników przez lata korzystaliśmy z dużego systemu produkcyjnego o powierzchni 280 m2. Jest to konwencjonalna linia produkcyjna, w której wykorzystywanych jest 26 maszyn i odbywa się sumarycznie 50 procesów. Ponieważ maszyny ustawione są szeregowo, zatrzymanie jednej powoduje zatrzymanie całej produkcji – dzięki temu wskaźnik OEE [Overall Equipment Effectiveness − Całkowita Efektywność Sprzętu, czyli międzynarodowy standard, pozwalający na mierzenie efektywności wykorzystania maszyn; przypis red.] jest niski. Dodatkowo sama linia zajmuje dużą powierzchnię i wymaga sporej liczby pracowników obsługi, zaś zmiany asortymentu są czasochłonne. Uznaliśmy, że czas na innowacje – zwłaszcza że obecnie produkty trzeba wytwarzać nie tylko masowo, ale też coraz częściej personalizować. To ostatnie musi jednak odbywać się przy zachowaniu wysokiej jakości i produktywności oraz niskich kosztów.
Co zrobiono?
Postanowiliśmy połączyć dwa rodzaje produkcji – masową zautomatyzowaną oraz personalizowaną – zachowując zalety każdej z nich. Wymagało to zaprojektowania od nowa procesów produkcyjnych, przy czym wiele z nich – np. montaż i testowanie – zostało połączonych. Nowa linia produkcyjna bazuje na wykorzystaniu trzech gniazd zrobotyzowanych, które de facto projektowane były równocześnie z samym produktem, tj. stycznikiem z serii MS-T. Do sterowania pracą robotów, serwonapędów oraz innych podzespołów wykorzystana nasza została platforma iQ. Do niej podłączone są również systemy wizyjne, używane do określania pozycji i układu pobieranych elementów, a także kontroli poprawności montażu wyrobów. Korzystamy również ze śledzenia produktów, używając kodów 2D, nadrukowywanych na obudowy.
Na potrzeby systemu stworzyliśmy szereg rozwiązań specjalizowanych. Przykładowo, uchwyt każdego robota wyposażony jest w czujnik siły do pomiarów nacisku wywieranego podczas montażu obudowy stycznika. Wdrożyliśmy też ciekawe rozwiązanie, zapewniające poprawność wkręcania śrub. Korzystamy tutaj z serwonapędów i czujników mierzących wartość momentu obrotowego – przekroczenie określonego poziomu oznacza, że śruba została źle wsadzona i należy przerwać proces przed jej dokręceniem. W ten sposób znacznie zredukowaliśmy uszkodzenia gwintów podczas montażu. Zmieniliśmy także proces inspekcji – zamiast stosować pomiary głośności pracy styczników, mierzymy ich wibracje – również korzystając ze zrobotyzowanego stanowiska.
W systemie korzystamy w większości z produktów Mitsubishi Electric, połączonych ze sobą siecią CC-Link IE. Informacje o produkcji i jej jakości są agregowane, a następnie realizowane do systemu nadrzędnego. Podobnie jak w zakładzie w Nagoi, operatorzy uzyskują na bieżąco informacje o procesach zaplanowanych i zrealizowanych, powodach zatrzymania oraz o zużyciu energii. Te ostatnie można wyświetlać w odniesieniu do celi produkcyjnej, urządzenia, a nawet do pojedynczego wyprodukowanego produktu.
W efekcie zmian liczbę procesów zredukowano do 23, a maszyn – do sześciu. Z kolei do obsługi systemu konieczny jest tylko jeden pracownik. Czas cyklu jest dłuższy niż poprzednio, ale dzięki rzadkim przypadkom zatrzymania całkowita produktywność wzrosła o około 30%. Udało się również uzyskać znaczną oszczędność miejsca – do 44 m2, przy czym proces rozwoju i wdrożenia systemu zajął dwa lata. Nowa linia pracuje równolegle z już istniejącą – z tej ostatniej nadal korzystamy przy dużych wolumenach produkcyjnych. Jednak w przypadku krótszych serii i częstych zmian elastyczność instalacji zrobotyzowanej jest nie do przecenienia. Dzisiaj w przemyśle, i dotyczy nie tylko naszego zakładu, coraz więcej wyrobów musi być personalizowanych, przez co rozwiązania takie jak omawiane będą spotykane coraz częściej.
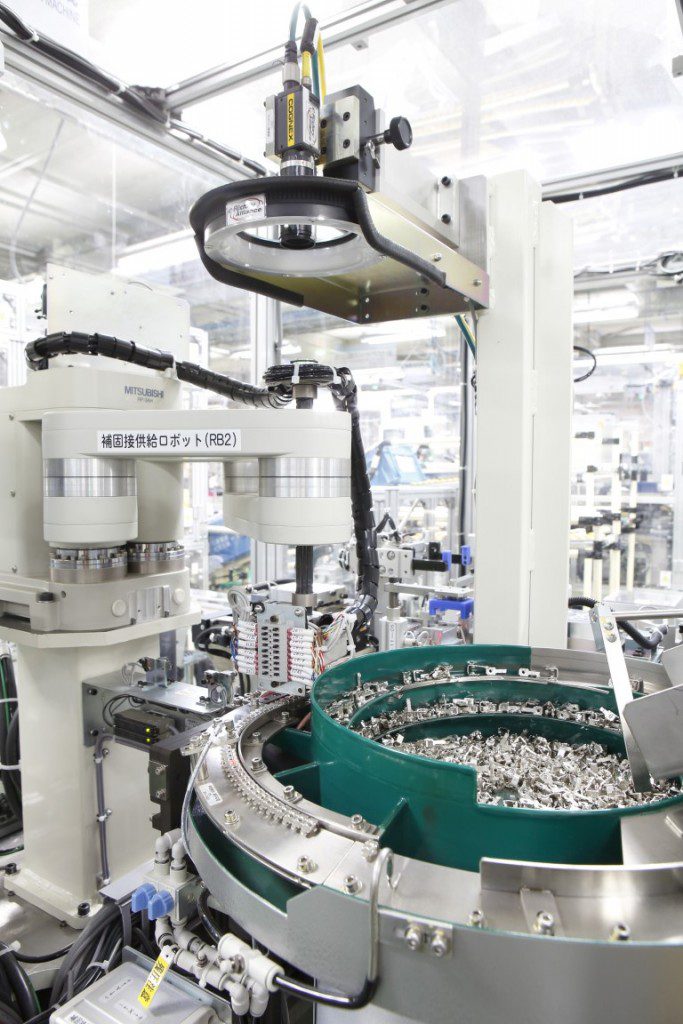
Szczegóły linii produkcyjnych w zakładzie w Kani – instalacja tradycyjna oraz nowe, zrobotyzowane stanowiska produkcyjne.
Jakie inne nowości wdrażacie w produktach?
W przypadku sterowania jest nią wspomniana platforma iQ, która jest w istocie systemem modułowym, integrującym sterownik logiczny, CNC, kontroler robotów, rozwiązanie Motion Control oraz interfejs do systemów IT. Jest ona programowana w jednym środowisku, co w połączeniu z parametrami i wysokim poziomem integracji zapewnia szybkie tworzenie oraz uruchamianie złożonych systemów, a także obniżanie kosztów ich przyszłego użytkowania. Warto dodać, że już w momencie premiery platforma objęta była blisko pięćdziesięcioma patentami.
Od wielu lat oferujemy również sieć CC-Link IE, która pozwala na transmisję danych z prędkościami do 1 Gb/s. Gdy w zeszłej dekadzie wprowadzaliśmy ją na rynek, wielu klientów pytało nas, do czego potrzebna będzie w maszynach sieć o takiej przepustowości. Dzisiaj, w dobie przetwarzania zbiorów Big Data, przesyłanie dużych ilości danych stało się konieczne nie tylko w sieciach IT, ale też w zastosowaniach przemysłowych.
Wiele nowości i de facto główną grupę naszych patentów stanowią rozwiązania napędowe. Przykładowo, oferujemy przemienniki częstotliwości z technologią OEC [Optimium Excitation Control – innowacyjna technologia optymalnej kontroli wzbudzenia, pozwalająca na maksymalne oszczędności energii; przypis red.], która zapewnia wytwarzanie w silniku optymalnej wartości strumienia magnetycznego. W przypadku silników realizujemy zaś nasze motto „easy to use, easy to make”. Wyroby te są coraz mniejsze przy zachowaniu parametrów mechanicznych, a ich produkcja coraz bardziej efektywna. Stworzyliśmy tu m.in. technologię otwartego statoru, która pozwoliła nam zrobotyzować proces nawijania uzwojeń.
W standardowe produkty wbudowujemy również rozwiązania z zakresu e‑F@ctory. Z naszych PLC można przesyłać dane bezpośrednio do systemu SAP (zintegrowany system informatyczny), bez pośrednictwa komputera. Z kolei serwonapędy pozwalają bezpośrednio, tj. bez stosowania dodatkowych czujników, monitorować stan systemów mechatronicznych. Mierzą one prędkość i moment obrotowy serwosilników, wibracje i inne parametry mechaniczne, dzięki czemu obsługa może bazować na predykcyjnym utrzymaniu ruchu.
W branży automatyki przemysłowej w Europie wiele uwagi poświęca się rozwiązaniom w zakresie energooszczędności. Jaką funkcję pełni ten aspekt w Waszej strategii rozwoju produktów?
Jest on bardzo istotny, zresztą nie tylko dla nas, ale praktycznie dla każdej tutejszej firmy. Japonia nie ma prawie żadnych surowców naturalnych, a większość surowców energetycznych musieliśmy przez długi czas importować. Wymuszało to szukanie energooszczędności – również w przypadku produktów automatyki. Dodatkowo, ze względu na niewielką dostępną przestrzeń mieszkalną, bardzo istotnym czynnikiem zawsze była oszczędność miejsca i miniaturyzacja urządzeń.
Oszczędność energii umożliwiamy nie tylko w przypadku produktów takich jak omawiane wcześniej napędy, ale też na poziomie systemowym. Możemy zaoferować zintegrowane rozwiązanie bazujące na połączonych w sieci sterownikach oraz modułach EcoWebServer III, które służą do akwizycji danych o wykorzystaniu energii. Dostarczamy również samodzielne mierniki, zaś po stronie software’u – oprogramowanie do zarządzania zużyciem energii oraz jego raportowania.
Naszym referencyjnym obiektem jest tutaj zakład Fukuyama Works. Wdrożyliśmy tam kompleksowy system zarządzania pracą maszyn oraz samym obiektem, który zapewnia nam roczne oszczędności, wynoszące ponad milion dolarów. W Fukuyama Works prowadzimy też regularnie szkolenia dla klientów w zakresie zintegrowanego zarządzania energią w zakładach produkcyjnych.
Jak z Waszych doświadczeń korzystać mogą klienci europejscy? Jaka jest aktywność Mitsubishi Electric na Starym Kontynencie?
Europa jest największym rynkiem automatyki na świecie i produkowana jest tam spora część najnowocześniejszych maszyn. Z tych powodów region ten jest dla nas zdecydowanie interesujący. Jako firma japońska zawsze jednak spoglądaliśmy na branżę przez pryzmat Azji, stąd też w Europie mamy cały czas jeszcze wiele planów rozwojowych. Ich realizacja w ostatnich latach jednak przyspieszyła – wzmocniliśmy naszą organizację, mamy więcej oddziałów, usprawniliśmy również logistykę.
Współpracujemy ponadto z europejskimi organizacjami branżowymi – m.in. w zakresie standardów sieciowych. Pomimo że jesteśmy promotorami rozwiązań bazujących na szybkiej i redundantnej sieci CC-Link IE, lokalnym klientom oferujemy też wersje urządzeń z komunikacją EtherCAT, Profinet i inną. Chcemy połączyć możliwość korzystania z japońskich technologii przy jednoczesnym zapewnieniu kompatybilności ze standardami regionalnymi.
Jesteśmy firmą globalną, która zapewnia wsparcie dla użytkowników maszyn i instalacji opartych o nasze rozwiązania, niezależnie od tego, gdzie są one wdrażane i wykorzystywane. Chcemy też działać lokalnie, będąc dla firm partnerem technologicznym, który dzieli się z nimi posiadanym know-how i nawiązuje długoterminowe relacje. Klientów z Polski zapraszamy do naszego FA Center w Balicach, gdzie w działaniu można zobaczyć nasze urządzenia i aplikacje systemów automatyki.
Dziękuję za rozmowę i możliwość odwiedzenia zakładów produkcyjnych.